RGM series: Rail-bound grinding machines, ideal for switches and long track sections
The abbreviation RGM stands for "Rail Grinding Machine" and refers to the series of rail-bound machines in accordance with category 4 as per EN 14033-1. These machines are optimally tailored to customer requirements and can be flexibly configured.
Contact our expertsRGM series
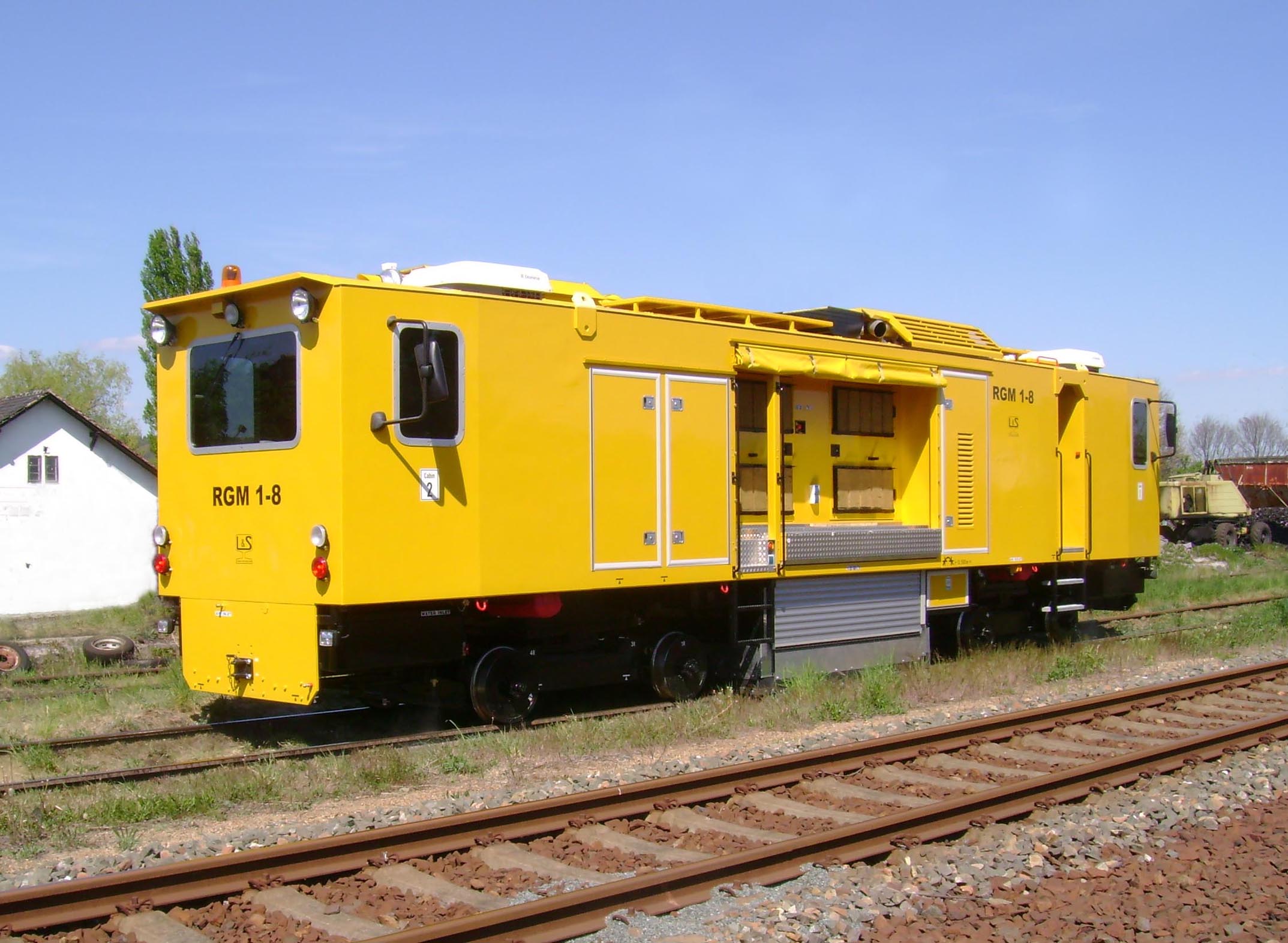
RGM 1-8
- Grinding modules: 8
- Grinding speed: 1.0 – 4.0 km/h
- Minimum curve radius: 30 meters
- Real-time measurement of transverse and longitudinal profile, EN 13231
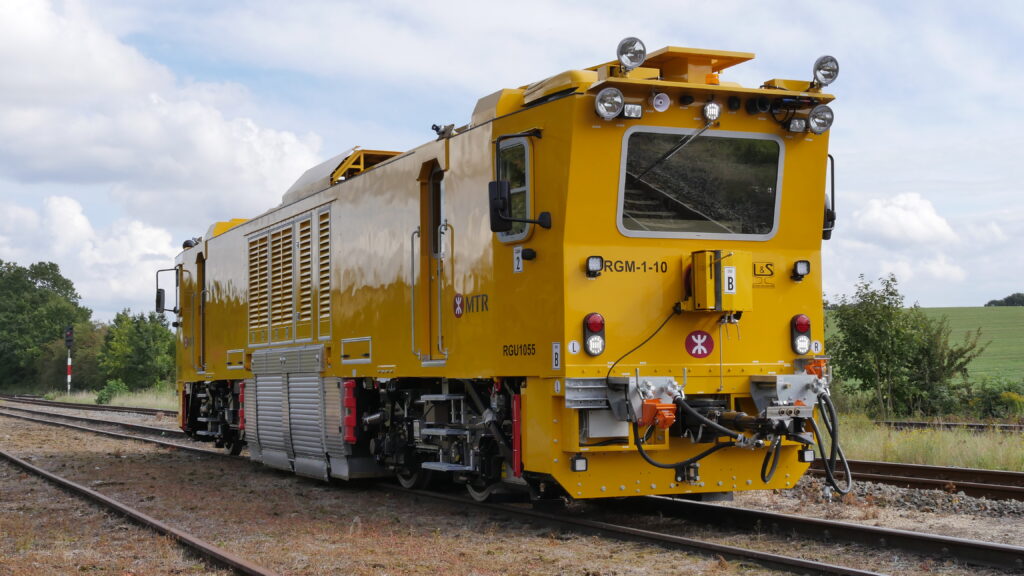
RGM 1-10
- Grinding modules: 10
- Grinding speed: 0.5 – 12.0 km/h
- Minimum curve radius: 60 meters
- Real-time measurement of transverse and longitudinal profile, EN 13231
- Automatic processing of turnouts, EN 13231
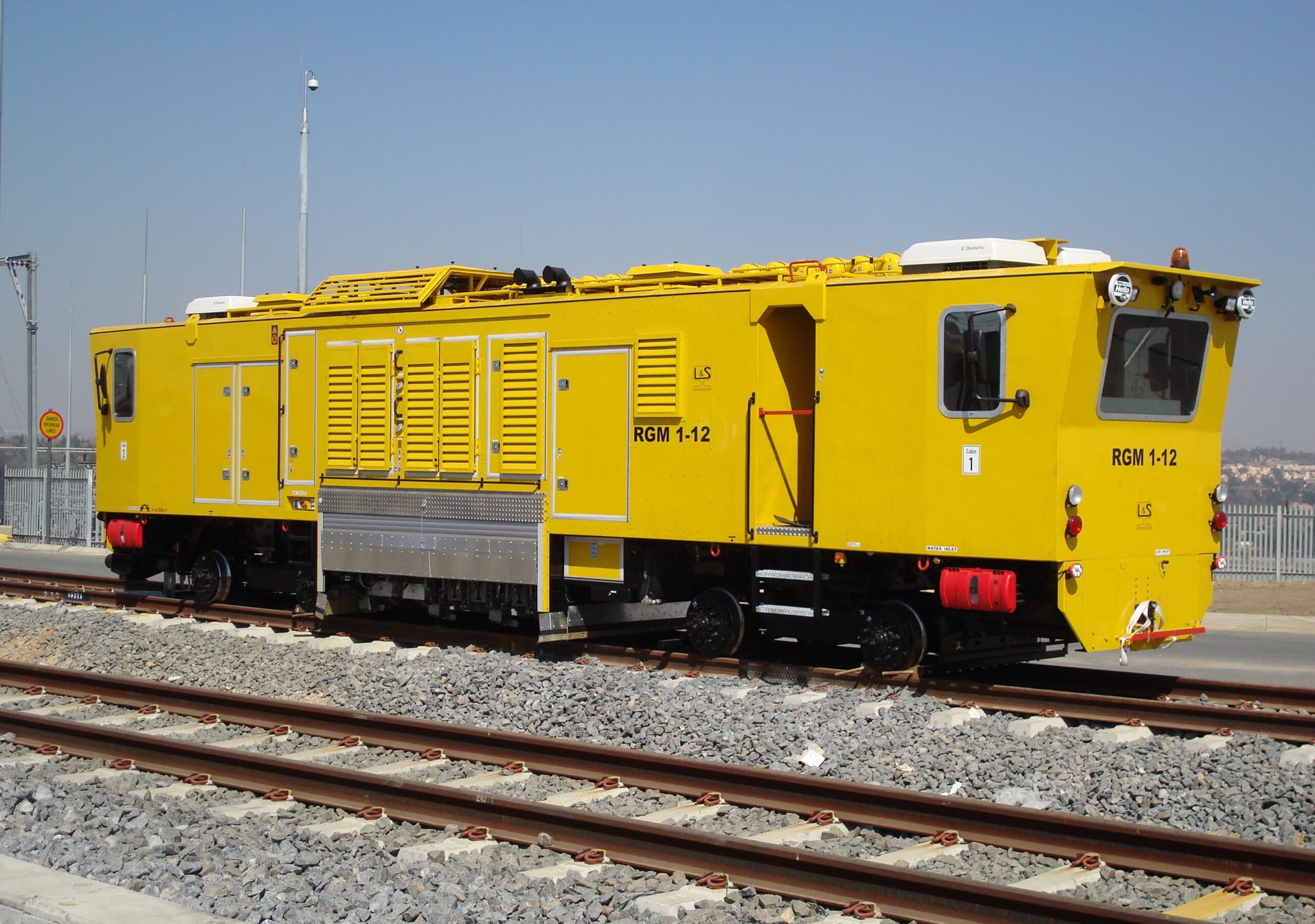
RGM 1-12
- Grinding modules: 12
- Grinding speed: 0.5 – 12.0 km/h
- Minimum curve radius: 60 meters
- Real-time measurement of transverse and longitudinal profile, EN 13231
- Automatic processing of turnouts, EN 13231
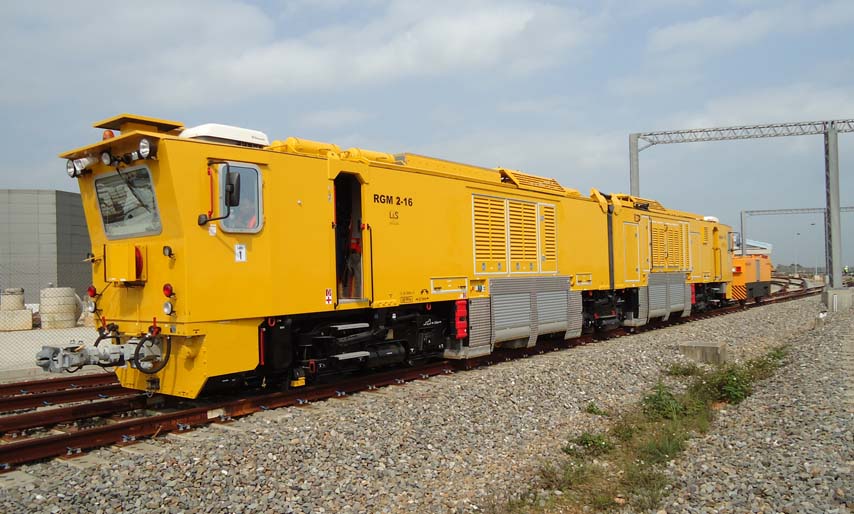
RGM 2-16
- Grinding modules: 16
- Grinding speed: 0.5 – 12.0 km/h
- Minimum curve radius: 80 meters
- Real-time measurement of transverse and longitudinal profile, EN 13231
- Automatic processing of switches, EN 13231
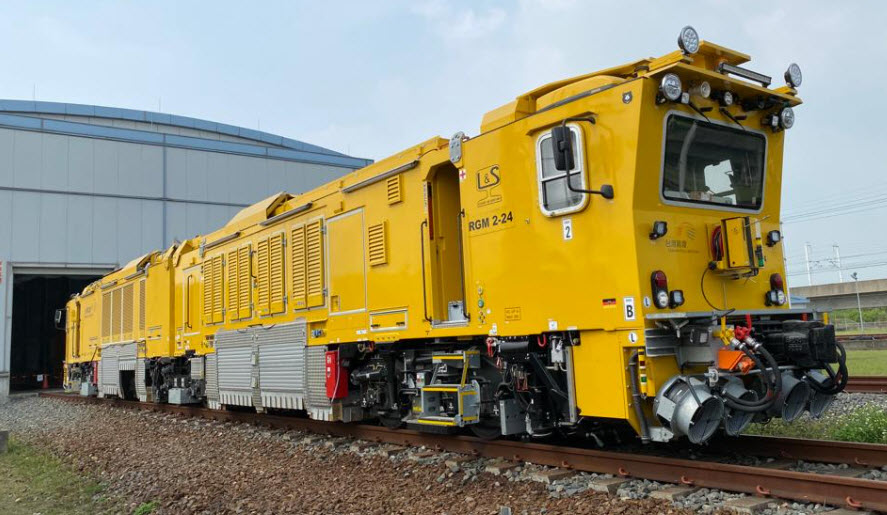
RGM 2-24
- Grinding modules: 24
- Grinding speed: 0.5 – 12.0 km/h
- Minimum curve radius: 50 meters
- Real-time measurement of transverse and longitudinal profile, EN 13231
- Automatic processing of turnouts, EN 13231
Application
- Automatic turnout processing
- Maintenance of long track sections
- Reprofiling of rails in tunnels
- Processing of level crossings
- Processing of grooved and Vignol rails
Performance
- Optimum adaptation to specific application scenarios
- Maximum precision thanks to state-of-the-art technology
- Environmentally friendly and safe operation
- Fast transportation to the construction site by rail
- Proven quality and reliability from L&S
- Maximum comfort for the operating personnel
Up to 12 grinding modules in a one-carriage design or 24 grinding modules in a two-carriage design can be set independently of each other via a computer-controlled grinding process and are capable of automatic turnout grinding.
All actuators and drives of the grinding technology operate pneumatically or electrically, which minimizes the risk of fire and makes a significant contribution to environmental protection.
Thanks to the use of customer-specific signaling equipment and the corresponding interface, these machines can be integrated into the train formation or move fully independently on the rail network.
A UIC air brake system ensures the necessary safety.
Air-conditioned and generously proportioned cabins at each end of the machine provide the operating personnel with a comfortable workplace.
With a powerful integrated generator, the machine can work autonomously for several days if required and offers an optimum balance between efficiency, availability and environmental protection thanks to the EU 2016/1628 Stage V emissions standard.
As an option, the machines are equipped with various laser measuring systems for measuring the transverse rail profile, longitudinal rail profile and roughness. If required, a water system with a capacity of several thousand liters can be installed, which can be used for firefighting and track cleaning.
As an option, the machines are equipped with various laser measuring systems for measuring the transverse rail profile, longitudinal rail profile and roughness. If required, a water system with a capacity of several thousand liters can be installed, which can be used for firefighting and track cleaning.